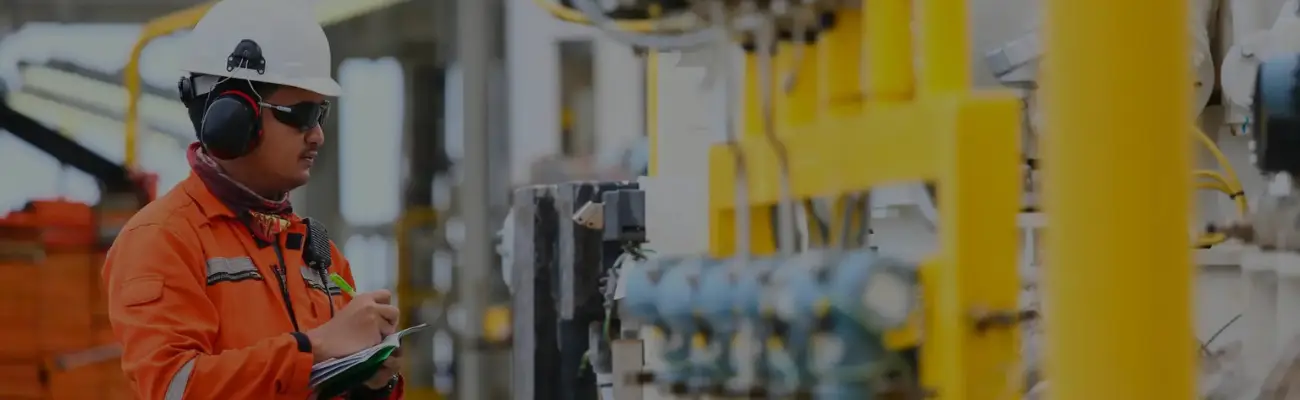
Measuring water percentage in oil is the key factor in determining the quality of oil available for sale.
Numbers of technologies are available for measuring water in oil or water-cut. Coriolis densitometers, microwave analyzers, and infrared spectrometers all have application strengths in certain niches. However, capacitance-based water cut measurement is the most common due to its comprehensive applicability.
Water-Cut measurement through Capacitive ( RF Admittance ) Sensors
Capacitive measurement
The difference in dielectric constant between water (k 80) and oil (k 2.3) determines the huge difference in cumulative measurement of capacitance. The more water present in the oil, the higher its capacitance.
The sensing element and the surrounding wall form a concentric capacitor. To measure the capacitance, the system transmits Radio Frequency (RF) voltage to the sensing element. From the measured capacitance, water percentage is calculated as it has a predictable relationship with the material’s properties.
The water dielectric constant varies little in response to the temperature changes. Therefore, system electronics can compensate for temperature-dependent changes in the oil-phase dielectric constant.
Water-cut measurement through the capacitive principle has many advantages.
- High temperature and pressure capabilities (up to 450°F and 1,500-psi)
- Non-epoxy coatings that are resistant to even erosive, sand-bearing mixtures
- Relative immunity to paraffin build-up
- Insertion probe assemblies that are easy to install and clean, and straightforward to calibrate.
The drawback is that when the water content in the oil-continues mixture increases. There is an inversion point when oil is dispersed in water rather than water dispersed in oil. At this point, the fluid becomes conductive. As a result, it makes the capacitor effectively shorted out. This process limits the measuring range to 0 to 50 % in light oil and 0 to 100% in heavy oil.
Other technologies can measure 0 to 100% range. But they are more complex and cost three to four times higher. Most oil field applications do not demand a 0 to 100% water cut range.
Separator control and optimization
The most common application for water cut is that thermal separator or heater treater. This application uses thermal energy in concurrence with a chemical injection or high voltage to break the oil-water emulsions.
Quality assurance capacitive-based water cut analyses, and another Radio Frequency probe are used to detect the electrical interface level between the oil and water phases for the final oil phase. Together, these measurements provide optimal control of the separation.
The water cut monitor helps determine the interface level position and the amount of chemical injection required to control the less well-behaved emulsion layer.
Automated Well Testing ( AWT )
The above section explains the productivity of many wells combined. AWT, in contrast, consists of a small batch-oriented vessel that is used to sequentially test the productivity of many of the wells per day. In this, a particular well is metered to the test vessel. Net oil is calculated by capacitive water-cut measurement, water level, water-oil interface level, flow rate, pressure, and temperature. Net oil is the amount of oil produced net of its basic sediment and water content.
Lease Automated custody transfer ( LACT )
It is the movement of oilfield production through the pipeline, truck rail cars, etc., which results in a change of ownership. The oil is typically sold through a lease automated custody transfer unit, which measures the flow rate and the composition of the oil. These LACT units or skids are designed as per the API standard. Measurement of water-Cut, Density, and volume flow measurement is crucial in determining the quality of the oil transferred.
RF Admittance interface level transmitter and an RF admittance (capacitive) water-cut monitor together can provide effective control of a thermal separation unit
Simplified Functional Diagram of a LACT unit
The accuracy of volumetric flow measurement is assured by periodic verification of the flow meter against the ± 0.2% master.
A capacitive water-cut analysis can monitor the maximum allowable limit of the water content in the oil. Water content exceeding the limits shouts down the transfer and diverts the oil back to its source for further processing.
- Separation Control
- Automated Well Testing (AWT)
- Lease automatic custody transfer ( LACT )
Capacitive water-cut analysis has a record of reliable and cost-effective performance on the above three applications.